News
Contact
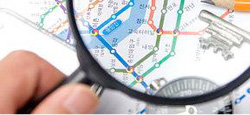
Zip:201602
Tel:021-57792777 / 021-57793388
Fax:021-57792555
Contacts:Mr.Lin / 13916662755
Mr.Zhang / 13801652830
QQ:2772215035
E-mail:dehonglyc@126.com
What are the process conditions of PBT injection molding?
1) the hygroscopicity of PBT is small, but it is sensitive to water at high temperature. During the molding process, the PBT molecules will degrade, the color will become darker, and the surface will produce spots. Therefore, the PBT should be dried normally.
2) PBT melt has excellent fluidity, so it is easy to form thin-walled and complex products, but pay attention to die overflow and nozzle salivation.
3) PBT has obvious melting point. When the temperature rises above the melting point, the fluidity of PBT will increase sharply, especially attention should be paid.
4) PBT molding has a narrow processing range, rapid crystallization during cooling and good fluidity, so it is especially suitable for rapid injection.
5) PBT has a large shrinkage and its shrinkage range, and the shrinkage difference in different directions is more obvious than other plastics.
6) PBT is very sensitive to the response of notches and sharp corners. In these positions, stress concentration is easy to occur, so that the bearing capacity is greatly reduced, and it is easy to crack when subjected to force or impact. Therefore, attention should be paid to this point in the design of plastic parts. All corners, especially the internal corners, should adopt arc transition as much as possible.
7) the elongation of pure PBT can reach 200%, so the products with small depression can be forced to demould from the mold. However, after filling with glass fiber or filler, its elongation is greatly reduced. If there is a depression in the products, forced demoulding cannot be carried out.
8) if possible, the runner of PBT mould should be short and thick, and round runner. General modified and unmodified PBT can be used in common flow channel, but glass fiber reinforced PBT can be used in hot flow channel molding.
9) the shear action of point gate and latent gate is large, which can reduce the apparent viscosity of PBT melt and is conducive to molding. It is often used gate, and the gate diameter should be larger.
10) the gate is facing the core cavity or core, which can avoid spraying, and make the remelting small when the molten material flows in the mold cavity. Otherwise, the product is easy to produce surface defects, and performance degradation.
Main injection molding conditions of PBT
1) barrel temperature. The selection of barrel temperature is very important for PBT molding, such as low temperature and poor plasticization, which will result in material shortage, depression, uneven shrinkage and lusterless. If the temperature is too high, the nozzle will salivate seriously, overflow the edge, darken the color and even degrade. Generally, the barrel temperature is controlled at 240-280 ℃, and the glass fiber-reinforced PBT is controlled at 230-260 ℃. The temperature of the nozzle should be controlled at 5 ~ 10 ℃ lower than that of the front section of the barrel.
2) mold temperature. Mold temperature is directly related to dimensional stability, warpage, molding cycle and crystallinity of products. PBT is easy to crystallize, even at room temperature, it also crystallizes quickly, so the mold temperature does not need to be too high, usually 40 ~ 60 ℃, while the mold temperature of glass fiber reinforced PBT is slightly higher, usually 60 ~ 80 ℃.
3) injection pressure. The melt viscosity of PBT is low and its fluidity is good. Medium injection pressure can be used, generally 60-90mpa, 80-100mpa for glass fiber reinforced PBT. Generally, the injection pressure increases with the increase of the thickness of the plastic part, but not more than 100MPa, otherwise it will make the demoulding difficult.
Previous: TUBOTECH & WIRE South America 2019